
When the city garbage to 8% annual growth rate, a set of data is triggering global concern – the global solid waste generated every day is enough to fill up 150,000 standard swimming pools. In this silent “garbage around the city” battle, the garbage shredder is from behind the scenes to the front of the stage, becoming an indispensable core equipment in the chain of solid waste treatment. It not only redefines the standard of garbage pretreatment, but also opens up new possibilities in the era of circular economy.
1、Breaker under the city of municipal waste
In the traditional waste treatment system, the environmental cost of direct landfill or incineration of mixed waste is increasingly visible. *The 2023 White Paper on Global Solid Waste Management* points out that unclassified shredded garbage reduces incineration efficiency by 15-30%, while increasing the risk of heavy metal leaching. The garbage shredder crushes all types of solid waste to uniform particles of 5-50mm by means of a high-torque blade system. This pre-treatment process allows subsequent sorting accuracy to be increased by more than 40%.
Measured data from an environmental protection industrial park shows that the metal recovery rate jumps from 62% to 89% for construction waste treated by the twin-shaft shredder, and the purity of wood materials reaches 93%. This physical dismantling revolution not only improves the value of resource recycling, but also extends the life of the landfill by 2-3 times.
2, the intelligent evolution of the core technology
modern waste shredder has broken through the traditional crushing concept, incorporating a number of innovative technologies:
Adaptive blade system: real-time adjustment of rotational speed through pressure sensors, automatic speed reduction protection when encountering metal and other hard objects
Internet of Things monitoring platform: more than 20 parameters such as bearing temperature, vibration frequency, etc. can be monitored, and the accuracy of fault warning reaches 98%
Modular design: quick replacement of different shapes of blades, and the processing range covers 12 major categories of materials such as plastics, tires, and e-waste
Quantum Series developed by a German equipment manufacturer A German equipment manufacturer has developed the Quantum Series shredder, which adopts gradient hardness blade technology, with the surface hardness reaching HRC62 and the core maintaining the toughness of HRC48, which extends the life of knives by 3 times. This “rigid and flexible” design concept is the epitome of modern environmental protection equipment technology iteration.
3, the key pivot point of the circular economy
In a renewable resources base, after shredding PET plastic bottle chips, cleanliness reached food-grade standards, the selling price per ton compared with the traditional process to enhance the 1200 yuan. Behind this jump in value is the material standardization revolution brought about by the shredder – the uniform fragment size makes the cleaning efficiency increase by 70% and the granulation energy consumption decrease by 25%.
4. The ecological benefit matrix of the garbage shredder has been clearly shown:
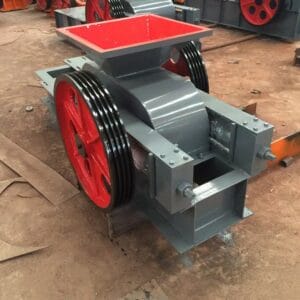
Reducing landfill space occupation: the annual processing capacity of one 300HP equipment is equivalent to the landfill capacity of 30 standard soccer fields
Reducing carbon footprint: each ton of crushed garbage can reduce dioxin emissions from incineration by 45%
Creating a new industrial chain: giving rise to more than 10 emerging industries such as recycled plastics, RDF fuel, and so on
Fourth, the golden rule of equipment selection
In the face of the market’s more than a hundred types of shredder models, the purchaser needs to grasp the three key Dimension:
Material Characteristics Matrix: establish a three-dimensional evaluation model of hardness, toughness and moisture content
Energy consumption ratio formula: processing capacity (kW-h/t) = motor power ÷ actual output
Full life cycle cost: including maintenance cycles, wearing parts replacement frequency and other hidden costs
Comparative tests of an automobile dismantling enterprise show that the shredder with hydraulic drive system reduces energy consumption by 18% compared with the traditional direct-driven motor, and increases production capacity by 22% when processing toughness A comparative test of an automobile dismantling company showed that a shredder with a hydraulic drive system consumes 18% less energy and has a 22% higher capacity when processing tough materials than a traditional motor-direct drive type. The choice of this technology route directly affects the project’s return on investment cycle.
5, the future track of the innovation picture
With the penetration of AI technology, intelligent shredding system is rewriting the rules of the industry:
The visual recognition system can automatically identify the type of material and switch the optimal shredding mode
The digital twin platform enables accurate prediction of tool wear
Blockchain technology traces the processing of each batch of shredded material
The latest case of an intelligent waste station in Singapore shows that the shredder equipped with machine learning algorithms automatically optimizes the combination of blades by analyzing the historical data, which has increased the recovery rate of precious metals from e-waste by 5 percentage points. This evolutionary model of human-machine collaboration is opening up a new dimension in solid waste resource utilization.
In this green change, the garbage shredder has transcended the simple mechanical concept and become a technological bridge connecting waste and renewable resources. From the sparks flying in the crushing cavity, what we see is not only the collision of metal and blades, but also the deep dialog between human wisdom and ecological challenges.